Top 5 Problems Inspectors Find with Water Heaters
Water heaters are crucial to every home, but they are prone to problems that disrupt daily life and can lead to costly repairs. A Professional Home Inspector at Boxer Inspections LLC, often encounter these issues during their home inspections. Below are the top five water heater issues and how they’re addressed, incorporating insights from professional home inspections.
1. No Hot Water or Inconsistent Heating
This is one of the most common complaints during water heater inspections in Sugar Land. The problem often stems from a malfunctioning heating element, a broken thermostat, or an interrupted power or gas supply. Inconsistent water temperatures can also signal sediment buildup, which reduces efficiency.
- Advice from Home Inspectors Sugar Land TX: A certified home inspector in Sugar Land, TX, recommends scheduling regular water heater maintenance. Professionals can flush the tank to remove sediment and inspect components for wear.
2. Leaks Around the Water Heater
During plumbing inspections in Sugar Land, leaks around the water heater often indicate loose connections, a faulty pressure relief valve, or a corroded tank. Left unchecked, leaks can cause significant water damage.
- Recommendation from a Sugar Land Property Inspection Experts: Address leaks immediately by tightening connections and replacing faulty parts. If corrosion is severe, replacing the unit may be necessary.
3. Strange Noises (Rumbling, Popping, or Banging)
Unusual noises are frequently noted during Sugar Land real estate inspections. These sounds often result from sediment buildup at the bottom of the tank, which traps water and creates rumbling or popping when heated.
- Tip from the Best Home Inspectors in Sugar Land: Regularly flush the water heater tank to remove sediment. This preventative step not only eliminates noise but also extends the lifespan of the unit.
4. Discolored or Smelly Water
Foul odors or discoloration are red flags that often appear during water heater inspections in Sugar Land. Rusty water is usually caused by a failing anode rod, while bacterial growth in the tank may produce a sulfur-like smell.
- Solution from Certified Home Inspectors in Sugar Land TX: Replace the anode rod if rust is present. For odors, a hydrogen peroxide treatment can sanitize the tank and restore water quality.
5. Improper Installation or Lack of Maintenance
Improper installation is a significant issue uncovered during professional home inspection services. Common mistakes include inadequate venting, missing safety features like pressure relief valves, corrosion, or poor placement. Lack of maintenance, such as neglecting to flush the tank or test valves, compounds these problems.
- Insight from an Affordable Home Inspector: Ensure installations are performed by licensed professionals and schedule annual maintenance. A properly installed and maintained water heater operates more safely and efficiently.
Why Choose Professional Water Heater Inspection in Sugar Land?
Water heater maintenance in Sugar Land is essential for preserving system efficiency and preventing costly breakdowns. Partnering with Boxer Inspections LLC ensures that potential issues are identified early, saving homeowners time and money.
For the best home inspector in Sugar Land, Tx, contact the Professional Home Inspector at Boxer Inspections LLC who offer comprehensive and affordable home inspections. From plumbing inspections to overall property evaluations, these experts provide the peace of mind every homeowner needs.
Final Thoughts
Water heater problems are common but manageable with regular inspections and maintenance. Whether it’s addressing leaks, flushing sediment, or ensuring proper installation, taking proactive steps can extend the life of your water heater and improve its performance.
If you’re due for a water heater inspection or suspect an issue, contact the Professional Home Inspection team at Boxer Inspections LLC. Certified experts can diagnose and resolve issues efficiently, ensuring your home’s systems operate at their best.
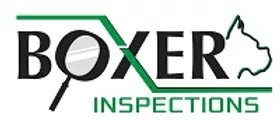
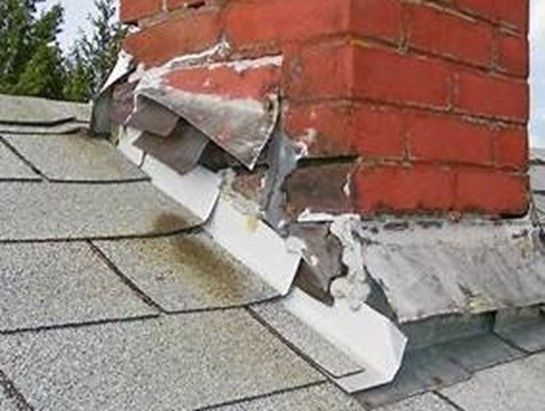
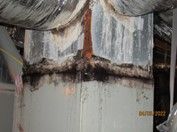
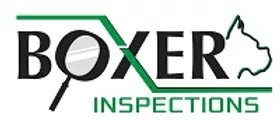
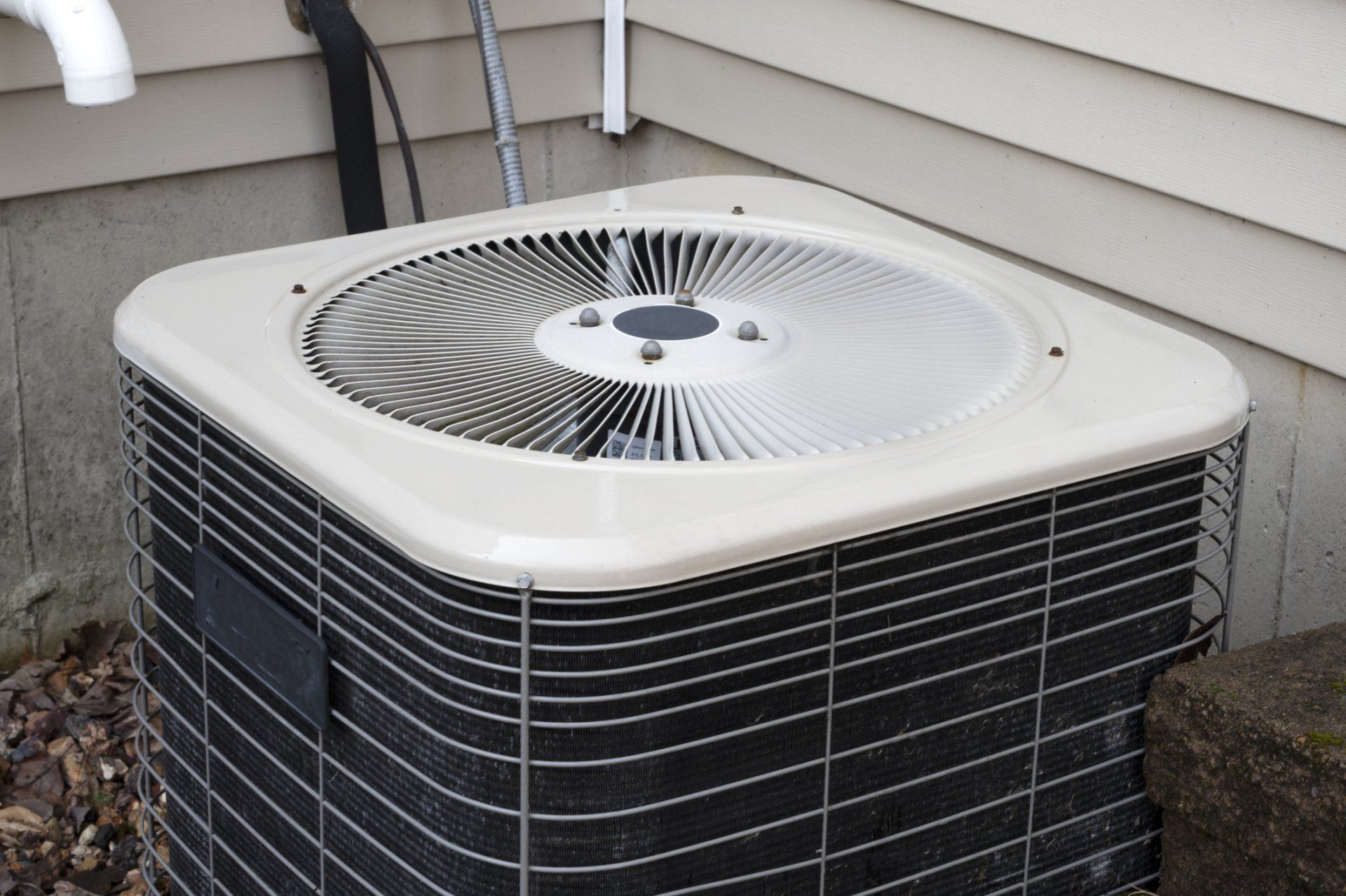
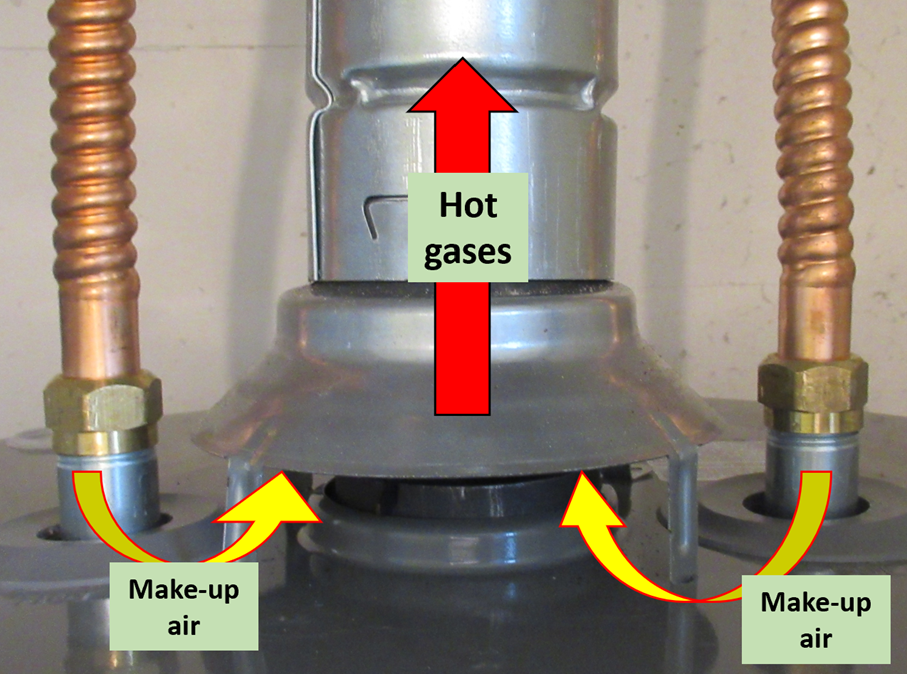